Architect – and U of T alumnus – designs ‘healthier’ temporary ICUs for COVID-19 patients
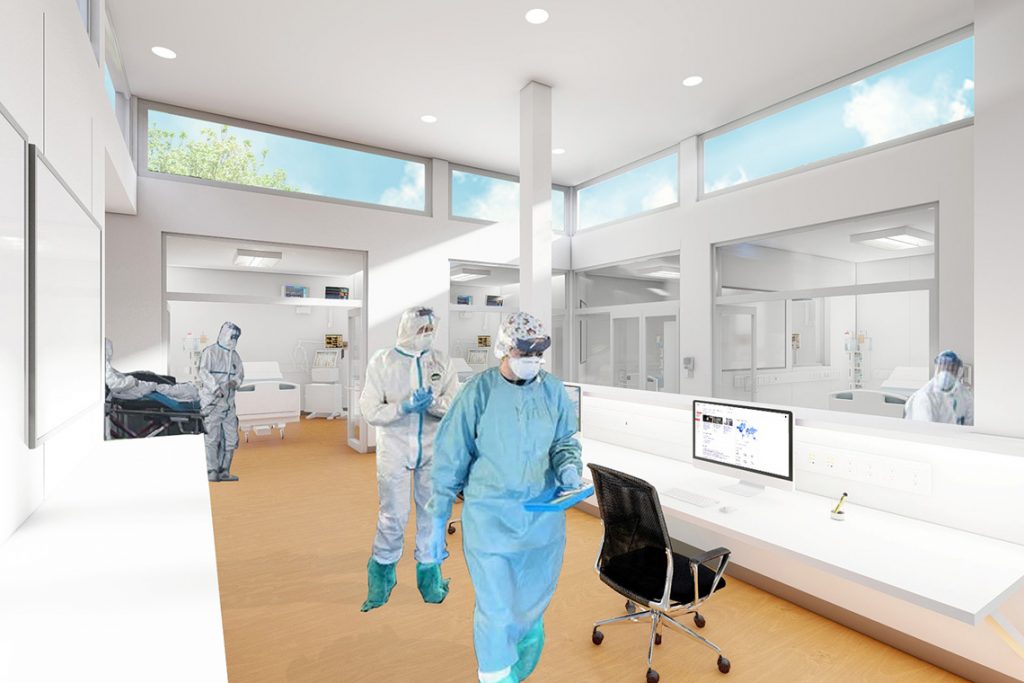
They went from a conversation on a Thursday morning to blueprints on Monday and a full-scale prototype built five days later. University of Toronto alumnus Tye Farrow, who graduated with a degree in architecture in 1987,and friend Ray Arbesman moved quickly to design temporary intensive care units in response to the COVID-19 pandemic.
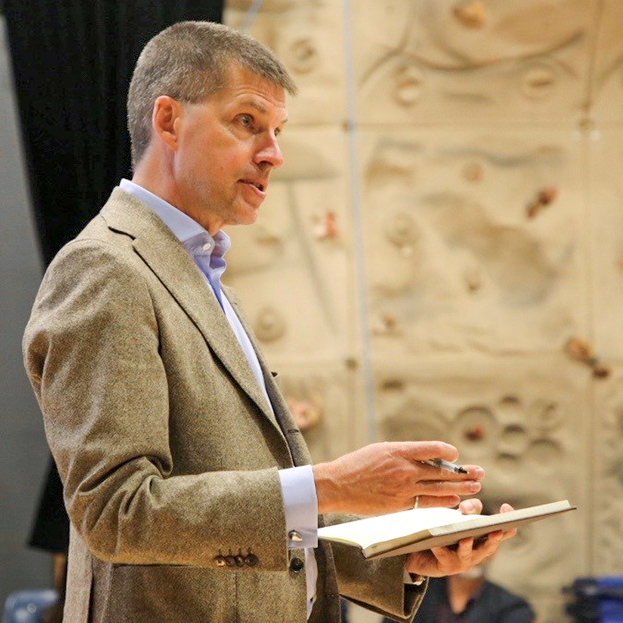
Farrow (left), who is the senior partner at Farrow Partners Inc. and the current president of the U of T Alumni Association, is known for creating buildings that wrap health-promoting features into their design. Arbesman is the founder of Nucap Industries, a global technology company, and the inventor of a novel mechanical system that can bind building materials together.
Together, they’ve developed Solace Rapid Assembly – High Performance COVID-19 Inpatient Bed Solutions, and they’re hoping the project could soon help hospitals around the world that are struggling to care for COVID-19 patients.
“Our goal has been to create solutions that are faster, cheaper, smarter, safer, more adaptable to individual hospital needs and importantly – healthier,” says Farrow.
Farrow founded the Cause Health movement to promote designs that nurture complete wellness, incorporating environmental sustainability, cultural sensitivity, a sense of purpose and health-boosting features such as natural materials, fractal shapes, and sunlight.
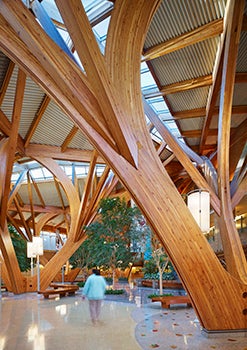
For example, Farrow designed the Carlo Fidani Regional Cancer Centre with tree-like structures that evoke a person reaching to the sky.
“Spaces can tune basic emotions and background bodily feelings from negative to positive,” says Farrow. “Neurophysiologists call the principle ‘neural mirroring’ – we model, or feel into, feelings we observe in another person.”
He adds that a building environment creates a similar response, so the reaching structures in the Mississauga hospital seek to generate optimism, as well as a sense of life and growth, and an uplifting feeling that you are somewhere special and purposeful.
Farrow is currently earning a master’s degree in neuroscience applied to architecture and design – a field so specialized “I believe I will be the only architect in Canada with this degree,” he says.
“There is scientific evidence that space can be an accelerant or leave us numb. And the human dimension connecting space and performance for medical staff and patients alike is at the top of my mind.”
Farrow’s design for the ICU structures is based on an innovative, never-before used building technique: wood blocks laminated with metal instead of glue. Arbesman, a U of T donor, initially invented the fail-safe, velcro-like technology to build safer car brake pads, but began collaborating with Farrow on possible construction uses about five years ago.
The resulting blocks are as strong as concrete, but lighter and as easy to assemble as Lego. Even unskilled volunteers could build one of the 12-bed ICU units on a parking lot or vacant lot in a few hours, according to Farrow.
Features such as clerestory windows to introduce natural light are designed to lower patient and staff stress, while the unit’s wraparound logistics corridor is environmentally controlled so that workers who service mechanics, electricity and medical gases remain isolated from patient areas.
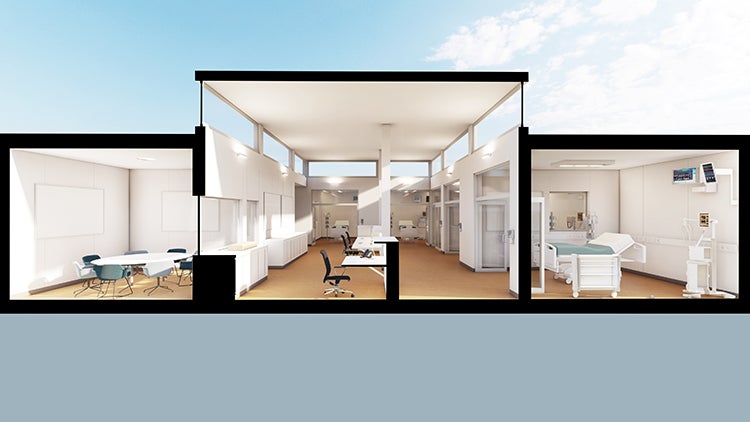
Farrow was inspired to improve on other temporary hospital solutions he’d seen on the news. “The environments we build to support our medical staff and patients need to be the meal equivalent to a fruit-, vegetable- and protein-enhanced energy drink smoothie,” he says, “giving you mental energy and clarity, physical strength and resiliency and mind comfort; an accelerant that will help you succeed under stressed conditions.”
Solace launched on April 23. “We already have interest from a range of different organizations in Canada, the U.S. and Israel,” says Farrow. “People are looking at it for the COVID-19 ICU responses, but because it is permanent in character, yet can also be disassembled easily, jurisdictions are also looking at it for other related uses that will need a longer shelf-life solution as we move into the winter.”
“I thought that the grip timber block solution was perfect as it could give a rapid response solution that could be designed to any medical special need, versus a fixed size as with shipping container structures,” he says. “And we can create an enhanced environment for staff and patients alike.
“Working on the project has been very stimulating and it’s satisfying that we will also be able to do our part.”